Water in Your Air Compressor Lines? Here's How To Stop It
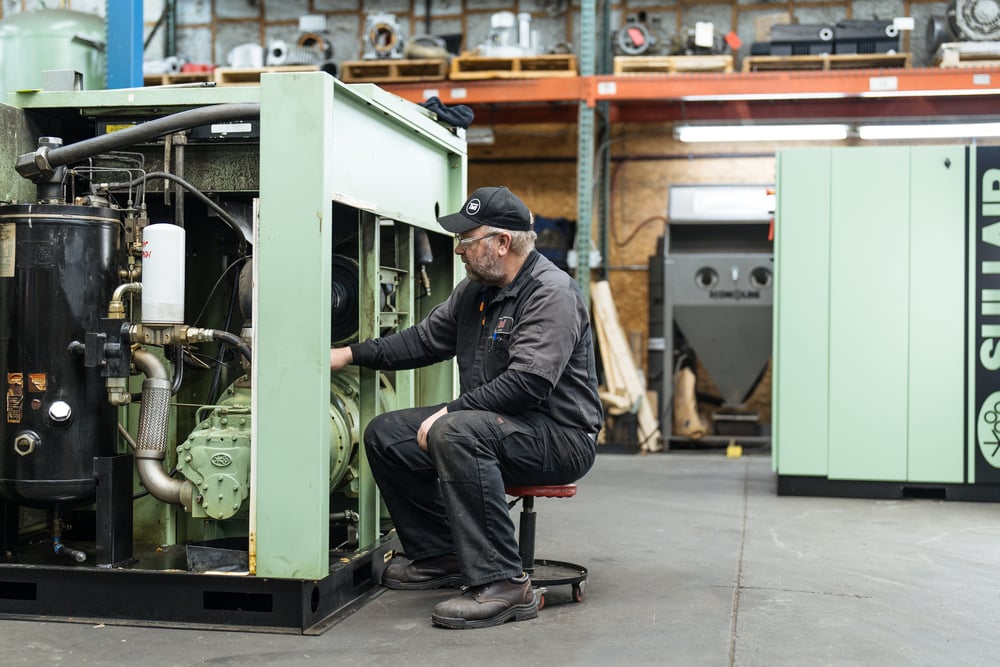
Water in your compressed air lines isn’t just annoying—it can lead to costly equipment damage, unexpected downtime, and poor product quality. Whether you’re running pneumatic tools or powering sensitive manufacturing processes, excess moisture in your air system can throw a serious wrench in your operations.
Here’s the thing: the water isn’t collecting inside your air compressor itself. It’s building up in your distribution piping. That’s because as compressed air cools while traveling through your system, the water vapor in the air condenses into liquid. That moisture can cause rust, corrosion, and performance problems if not properly managed.
In this blog, we’ll walk through why moisture ends up in your air lines, why it’s a problem, and what you can do to remove it—and prevent it from coming back.
Why Is There Water in Your Compressed Air Lines?
Air always contains some moisture—even if you can’t see or feel it. When ambient air is compressed, the water vapor in it becomes more concentrated. This is a natural part of the compression process, but it creates a challenge. The hotter and more humid the environment, the more water ends up in your system.
As the compressed air travels through your piping, the temperature starts to change. When warm, moisture-laden air cools down, water vapor condenses into liquid. That’s when water begins to collect inside your distribution lines, especially in low points or areas where air movement slows.
Why It’s a Problem
Water in your compressed air lines isn’t just a nuisance—it can wreak havoc on your entire operation. Even small amounts of moisture can have significant consequences if left unchecked.
Water in air compressor lines can lead to:
- Damage to tools, machines, and equipment: Moisture can cause rust, clog components, and reduce the lifespan of pneumatic tools and air-powered machinery.
- Corrosion in piping and components: Water promotes internal corrosion in your air distribution system, leading to leaks, pressure drops, and expensive repairs.
- Poor product quality: In industries like food processing, pharmaceuticals, electronics, and painting or coating, even trace amounts of water can compromise product quality or lead to contamination.
- Increased maintenance and downtime: When water causes wear and tear or fouls your equipment, you’ll spend more time and money on maintenance and risk unplanned system outages.
Bottom line? Moisture is the enemy of efficient, reliable compressed air systems.
How To Remove Water from Your Compressed Air System
Keeping your compressed air system dry requires innovative design, the proper equipment, and regular maintenance. Here are five proven ways to reduce or eliminate water in your lines:
1. Drain Your Air Receiver Tanks Regularly
Your air receiver tank is one of the first places moisture collects. Draining it daily—or better yet, using an automatic drain valve—prevents water buildup that can work its way into the rest of your system.
2. Use Water Separators and Filters
Water separators are designed to remove bulk water from your compressed air before it enters the distribution piping. They’re typically installed just after the compressor and before dryers or point-of-use equipment. Pairing them with quality particulate and coalescing filters ensures cleaner, drier air reaches your tools and processes.
3. Install a Compressed Air Dryer
Dryers are one of the most effective ways to remove moisture from your air supply. There are several types of air dryers to choose from:
- Refrigerated dryers: Cool the air to condense and remove water—great for general industrial use.
- Desiccant dryers: Use a drying agent to absorb moisture, ideal for very dry air requirements or freezing environments.
- Membrane dryers: Use selective permeation to remove water vapor and are best for point-of-use or low-flow applications.
The right dryer depends on your industry, environment, and air quality standards. A compressed air expert can help you choose the best fit.
4. Maintain Proper Piping Design and Slope
Make sure your distribution lines are sloped correctly (typically about 1 inch per 10 feet) so water drains away from your points of use. Include drop legs with drains, and avoid dead-end runs where moisture can collect with nowhere to go.
5. Perform Routine Maintenance
Preventative maintenance is key to keeping moisture out—and your system running efficiently. Even the best equipment can’t do its job if it’s not maintained. Check your filters, separators, dryers, and drain valves regularly to ensure they function properly.
How TMI Compressed Air Can Help Maintain Air Systems
Dealing with water in your compressed air system? You don’t have to figure it out on your own. At TMI Compressed Air, we specialize in identifying and solving moisture issues before they turn into bigger problems.
Whether you need a high-performance air dryer, an efficient water separator, or a completely redesigned piping system, we’ll help you find the right solution for your specific setup. Our team offers custom system design, installation, and preventative maintenance plans to keep your system operating at peak performance.
When you partner with TMI, you get more than just quality products. You get expert guidance, responsive support, and a long-term commitment to keeping your compressed air system reliable and efficient.
Keep Moisture Out and Performance Up
Water in your compressed air lines doesn’t have to be an ongoing issue. With the right combination of drainage, filtration, drying, and system design, you can protect your equipment, reduce downtime, and maintain consistent air quality across your facility.
Contact TMI Compressed Air today for help designing or upgrading your system to stay dry and run efficiently. Our experts are here to ensure your compressed air setup works as hard as you do.