Selecting the Appropriate Air Compressor Control System
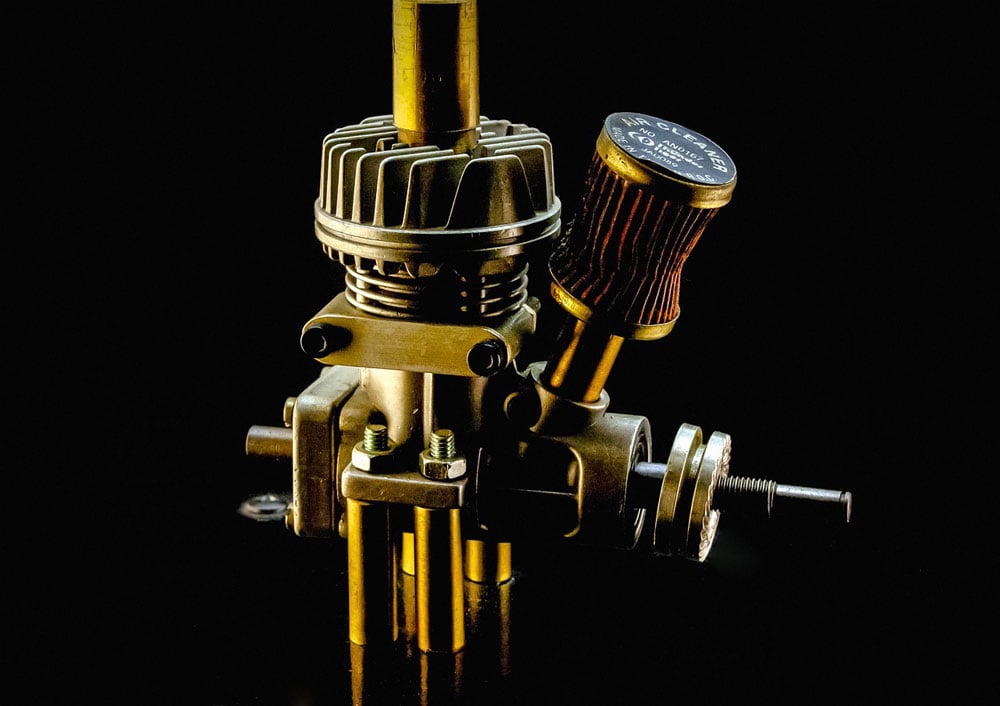
If you’re looking into a new air compressor for your company or facility, there are many considerations to make, from the type of compressor you choose to its size. Another important decision to consider is how your air compressor will be controlled. Your air compressor control system determines how much air you get, at what pressure, and when. It’s also a key factor in your air system’s overall efficiency.
If you’re new to air compressors and their control systems, this article takes a look at each available air compressor control system, breaks down its advantages and disadvantages, and gives you insight into which air compressors and applications that system is right for. Read on to discover the appropriate air compressor control system for your application:
Start/Stop Air Compressor Control System
The simplest control available, start/stop air compressor control systems do exactly what you’d imagine. They start when the machine’s pressure switch indicates that air pressure has fallen below the minimum discharge pressure, and they stop when the system has reached desired pressure.
In general, this air compressor control is best for applications with very low duty cycles. It is not well-suited to applications with frequent cycling; the constant starting will cause the motor to overheat.
The advantage of a start/stop air compressor control system is that you’re only drawing power when the compressor is needed. For low duty-cycle applications, this can contribute to significant energy savings.
The disadvantage of a start/stop air compressor control system is the compressor will have to compress a higher receiver pressure to allow air to be drawn from the receiver while the compressor is stopped.
Type of Compressor: Both reciprocating and rotary screw compressors can use start/stop air compressor controls.
General Application: Best used for applications with low duty cycles and intermittent use. Not an ideal option for a frequent cycling application.
Load/Unload Air Compressor Control Systems
Load/Unload air compressor control systems are also known as constant speed control. This type of air compressor control system allows the motor to run continuously, while unloading the compressor when discharge pressure is adequate.
The advantage of a load/unload air compressor control system is that you can eliminate the concern of overheating the compressor’s motor. Unlike the start/stop option, the motor keeps running, so you don’t have to worry about constant starts affecting the machine’s performance.
The disadvantage of a load/unload air compressor control system is that the system is constantly running. While this takes pressure off the motor, it’s not great for your facility’s energy bill. You might find that your compressor draws only slightly less power unloaded as it does loaded, while delivering no useful work.
Type of Compressor: Load/unload air compressor control systems are used for both reciprocating and rotary screw compressors.
General Applications: Can be used for a wide range of applications, but may not be the best option for large, industrial compressors that draw too much energy to justify the cost of their constant power draw.
Modulating Air Compressor Controls
Also known as throttling or capacity control, modulating air compressor controls work to progressively reduce air compressor output to match flow requirements. This is typically achieved by throttling or closing the inlet valve, reducing air to the compressor.
Modulating air compressor controls cannot be used on reciprocating or oil-free rotary screw compressors, and isn’t particularly efficient for oil or lubricated rotary screw air compressors.
The advantage of modulating air compressor controls is that you can vary output of your compressor to meet flow requirements. As pressure drops to a specified minimum, the compressor is unloaded.
The disadvantage of modulating air compressor control systems is that they’re not widely applicable. They’re best used for centrifugal air compressors, where they are both effective and efficient.
Type of Compressor: Modulating controls are best suited to centrifugal air compressors. They can also be used with lubricated rotary screw compressors, but are not the most efficient control option.
General Applications: Most often seen in large, industrial applications that must meet stringent air quality requirements. These applications typically require a centrifugal air compressor.
Dual/Auto Dual Air Compressor Control Systems
A dual or auto dual air compressor control system provides a greater range of control options for small reciprocating air compressors and for lubricant-injected rotary screw compressors.
Dual control air compressor control systems are used in small reciprocating compressors, and enable the operator to select either start/stop or load/unload controls, depending on the compressor’s application.
Auto Dual air compressor control systems are applied to lubricant-injected rotary screw compressors. They function to modulate the compressor to a pre-set reduced capacity. If the compressor has been running unloaded past a certain set period of time, the auto dual controls will stop the compressor.
The advantage of a dual or auto dual air compressor control system is flexibility. It allows the operator to select the control option that best suits the application. In the case of auto dual systems, it also protects your facility from excessive energy use, without putting stress on the motor of your air compressor.
The disadvantage of these systems is their limited application. They are not a control system that can be applied across a wide range of compressor types or applications.
Type of Compressor: Small reciprocating compressors and lubricant-injected rotary screw compressors.
General applications: Small industrial applications that do not need constant compressed air.
Variable Displacement Air Compressor Control Systems
Variable displacement air compressor control systems enable the compressor to adjust output pressure without starting or stopping, or loading and unloading. Generally, variable displacement air compressor control schemes combine a sliding or turn valve in conjunction with a modulating inlet valve to deliver more accurate, efficient pressure control.
The advantage of these systems is that they respond much better to changing output pressure requirements, without adding stress to the compressor with constant starting and stopping.
The disadvantage of a variable displacement air compressor control system is that it requires multiple control systems to function simultaneously. Pressure switch, variable capacity valve, and inlet valve must all be functioning together and properly for effective pressure control.
Type of Compressor: Variable displacement is applied to both reciprocating and rotary screw air compressors of various sizes.
General applications: Any industrial application, but is especially useful for compressed air systems that operate a compressor in two or more partially-loaded conditions.
Variable Speed Drive Air Compressor Controls
A variable speed drive is undoubtedly the most efficient air compressor control system available today. These control systems can hold compressor discharge pressure to +/- 1 psi ensuring your compressor is only working as hard as it has to. Air compressors with a variable speed drive make use of an electric motor that adjusts motor speed in response to system signals, to deliver the right amount of air, at the right time.
The advantage of a variable speed drive air compressor control system is that your air compressor only works as hard as it has to. This preserves the lifespan of the compressor while reducing its energy draw, helping to keep your facility at peak efficiency.
The disadvantage of a variable speed drive comes in the application. If your facility is only using the compressor with variable speed drive at lower speeds, you may not see the same energy savings as a compressor that’s used more constantly and closer to full capacity.
Type of Compressor: Variable speed drive air compressor control systems can be applied to a wide range of air compressor types, including reciprocating and rotary screw compressors.
General applications: Best used in mid-to-large-sized industrial applications, but can provide significant energy efficiency even to smaller applications that require constant compressed air.
Not sure which air compressor control system is right for you? Let the TMI team help. As compressed air efficiency experts, we’re always working to match our clients with the most efficient compressed air components. We can help you find the right air compressor control system for your application, that delivers you the best performance with high efficiency.
Contact TMI Air Compressors