What Is a Compressed Air Audit and Why Does Your Facility Need One?
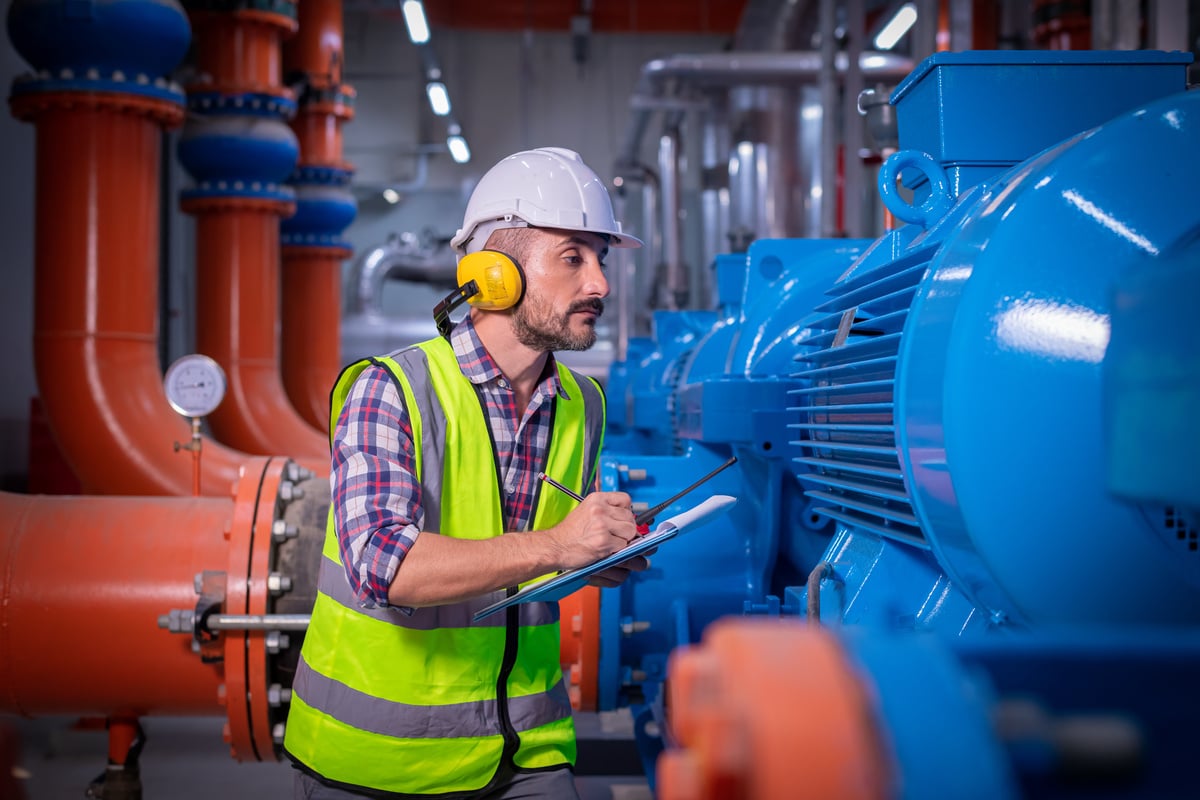
Compressed air systems are the backbone of daily operations in many industrial facilities. They power equipment and drive essential processes, so it’s critical they operate at peak efficiency.
However, hidden issues in these systems often go undetected until they cause significant disruptions. From small leaks to outdated components, these issues can quietly lead to increased maintenance expenses and even unexpected downtime.
A compressed air audit is a proactive way to identify and resolve these issues before they escalate.
This guide will walk you through everything you need to know about compressed air audits and how they set your facility up for long-term success.
What Is a Compressed Air Audit?
A compressed air audit is a systematic, in-depth assessment of your facility’s compressed air system. It’s designed to pinpoint inefficiencies, detect leaks, and uncover opportunities for energy savings. In other words, it’s a way to determine how much of your output is wasted.
Specialists carefully examine each part of the system—from compressors and piping to storage tanks and end-use equipment—to identify issues impacting performance and driving up costs.
The ultimate goal of a compressed air audit is to maximize the system’s efficiency, reliability, and cost-effectiveness.
An audit helps keep your system running smoothly and sustainably by addressing potential problems before they lead to costly breakdowns or energy waste. This proactive approach helps facilities achieve lower operational costs, longer equipment life, and a more dependable compressed air supply.
Why Does Your Facility Need a Compressed Air Audit?
Compressed air audits offer facilities a proactive way to uncover inefficiencies and improve system performance.
Here are three key reasons why a compressed air audit is essential for a successful business:
1. Improving Performance
Compressed air audits reveal hidden issues that can drain energy and inflate costs. Common culprits include leaks, poorly configured equipment, or unnecessary pressure drops. These issues waste energy, reducing the system's overall efficiency.
Addressing these problems can help facilities significantly lower their energy consumption and reduce the environmental impact of their operations.
2. Lowering Operational Costs
Fixing inefficiencies uncovered in a compressed air audit can substantially reduce utility bills and maintenance expenses.
For instance, a single air leak—even as small as a pinhole—can cost hundreds or thousands of dollars in wasted energy annually.
Pressure drops, another common issue, can force compressors to work harder, driving up electricity costs and wear on equipment.
3. Preventing Downtime and Extending Equipment Life
Unexpected system failures can lead to costly downtime and production disruption. Regular audits help prevent these interruptions by identifying issues before they escalate into major problems.
By catching potential issues early, routine audits can extend the lifespan of your equipment. In the long run, this minimizes the risk of breakdowns, reduces repair costs, and keeps your facility operating smoothly.
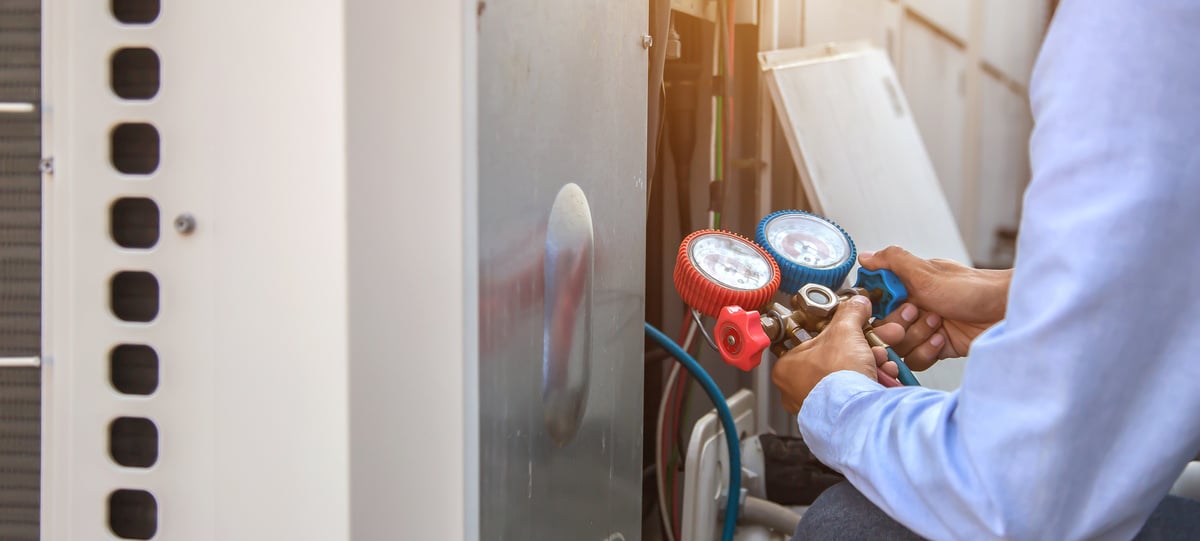
5 Steps of a Thorough Compressed Air Audit
At TMI Compressed Air, we take a thorough and systematic approach to every compressed air audit. Here’s how we conduct an optimized compressed air systems audit:
1. Site Survey
We start with a thorough walkthrough of the facility to assess the current setup and identify any visible issues. We then examine compressors, piping, storage tanks, and end-use equipment to fully understand your system’s structure and needs.
2. Measure Output
Then, we collect system performance data, including airflow, pressure, power usage, and energy efficiency. This data provides an accurate snapshot of how the system operates under normal conditions, making it easier to detect patterns and pinpoint inefficiencies.
3. Evaluate System Dynamics
We analyze the system’s configuration and operation to detect common problems. We’re looking for leaks, pressure drops, and flow restrictions. This step involves specialized equipment, like flow meters and leak detection tools, to ensure every detail is recorded.
4. Implement Recommendations for Improved Output
We will take corrective action to improve your system’s performance based on our findings. This might include sealing leaks, adjusting pressure settings, or replacing outdated components. Every recommendation is designed to enhance performance, reduce costs, and increase reliability.
5. Performance Verification
After implementing the recommended changes, we verify the system’s performance to ensure the improvements deliver the expected results. This may involve re-measuring outputs and monitoring the system over time to confirm sustained benefits.
How TMI Compressed Air Can Help
At TMI Compressed Air, we understand that no two facilities are the same, so we customize our compressed air audits to meet each client's unique needs.
Once the audit is complete, we don’t just walk away. We offer ongoing support to help you implement the recommended changes, ensuring that improvements are fully integrated into your system. With TMI Compressed Air, you can trust that your facility’s productivity, energy savings, and equipment reliability are in expert hands.
Don’t wait for issues to impact your operations—contact TMI Compressed Air today for a consultation and take the first step toward a more efficient, dependable compressed air system.